In the ever-evolving world of CNC milling machining, precision is not just a goal; it’s an absolute necessity. As industries demand tighter tolerances and more intricate designs, the right tools can make all the difference between flawless production and costly errors.
Among the myriad options available, three essential tools stand out, each playing a crucial role in enhancing both accuracy and efficiency. From advanced cutting tools that slice through metal with surgical precision to sophisticated software that streamlines the design process, the tools you choose can elevate your machining capabilities to unprecedented heights.
In this article, we will delve into these indispensable resources, exploring how they empower machinists to achieve remarkable results in their craft. Whether you’re a seasoned professional or an enthusiastic newcomer, understanding these tools could very well be the key to unlocking your potential in the realm of CNC milling.
High-Speed Spindle: Enhancing Cutting Efficiency
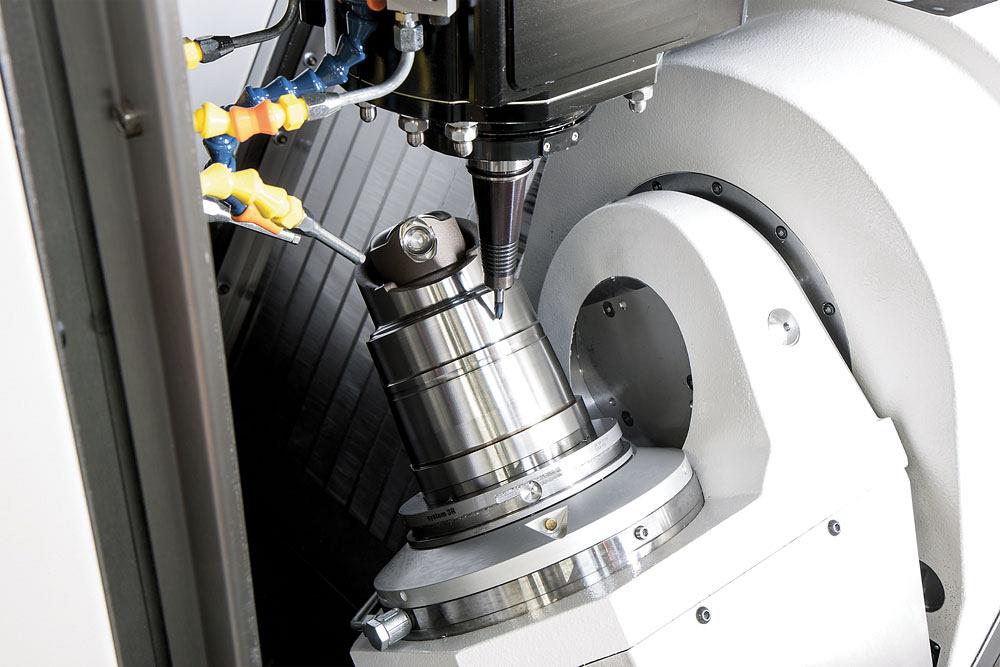
The high-speed spindle is a game changer in the realm of CNC milling, transforming the way machinists approach precision cutting. By enabling rotation speeds that can exceed 30,000 RPM, these spindles significantly elevate the cutting efficiency, allowing for faster feed rates and reduced cycle times.
This means that intricate designs, once deemed impossible due to time constraints, can now be tackled with ease. With their ability to maintain accuracy even at these high velocities, high-speed spindles minimize thermal distortion, resulting in superior surface finishes and tighter tolerances.
Consequently, they not only enhance productivity but also extend tool life, creating a virtuous cycle of efficiency and cost-effectiveness in the manufacturing process. As industries continue to demand higher precision and faster turnaround times, investing in high-speed spindle technology is not just advantageous—its essential for staying competitive.
Precision Tool Holders: Ensuring Stability and Accuracy

Precision tool holders serve as the backbone of stability and accuracy in cnc milling machining, ensuring that cutting tools are securely fastened and precisely aligned during operation. These fixtures, often crafted from high-quality materials, minimize vibration and thermal expansion, which can lead to errors and diminished tool life.
A properly calibrated holder not only enhances the performance of the tool but also significantly impacts the quality of the final machined product. Imagine the difference: in one scenario, a tool shifts ever so slightly, leading to irregular cuts; in another, with an impeccably designed holder, the tool remains steadfast, delivering flawless results time after time.
The interplay between the tool holder and the machining process is crucial—each component must work in harmony to achieve the desired precision, elevating manufacturing capabilities to new heights. Investing in superior tool holders is not merely an option; it’s a necessity for those aiming for excellence in their CNC machining endeavors.
Advanced CNC Software: Streamlining Workflow and Optimization
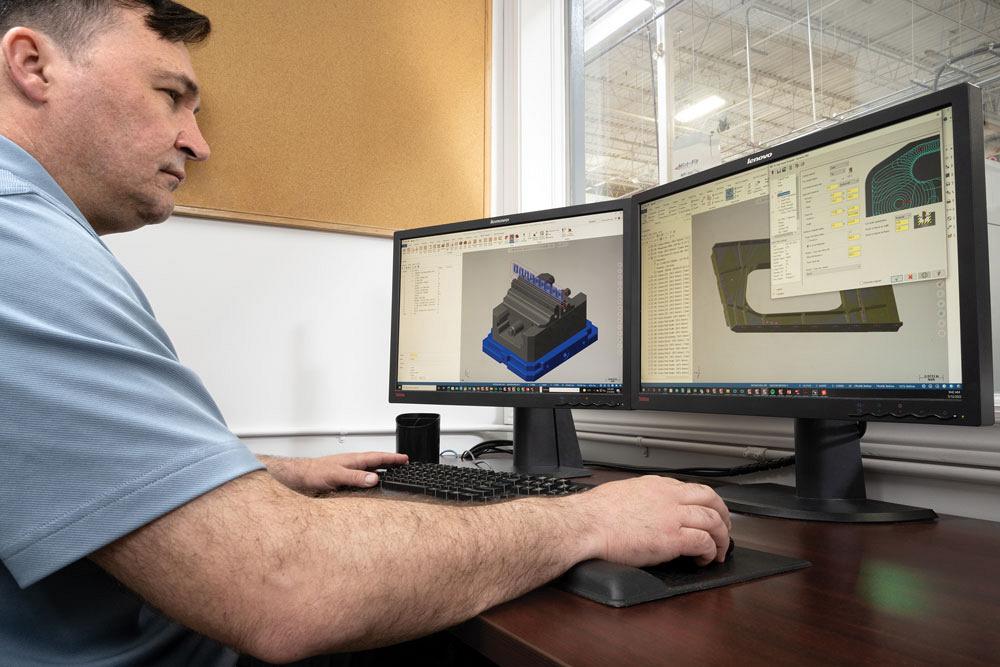
Advanced CNC software has revolutionized the landscape of precision milling machining, ensuring that workflows are not only streamlined but also optimized for maximum efficiency. Imagine a system that integrates seamlessly with machine tools, providing real-time monitoring and adaptive adjustments—a true game changer.
These sophisticated programs facilitate intricate design conversions, enabling operators to craft complex geometries with unparalleled accuracy. Meanwhile, intelligent algorithms help in predicting tool wear and optimizing cutting parameters, reducing downtime and material waste.
As operators harness the power of simulation features, they can visualize machining processes before they begin, minimizing errors and enhancing overall productivity. In a world where every second counts, advanced CNC software equips manufacturers with the technological edge necessary to stay competitive, pushing the boundaries of what’s possible in precision machining.
Conclusion
In conclusion, the integration of precision tools in CNC milling machining is pivotal for enhancing productivity and achieving high-quality outputs. By employing high-performance cutting tools, advanced tool holders, and effective coolant systems, manufacturers can significantly improve their machining processes, resulting in greater efficiency and precision.
As the industry continues to evolve, staying updated with the latest advancements in these essential tools will not only streamline operations but also foster innovation, ultimately leading to superior product outcomes and a competitive edge in the market. Embracing these tools will undoubtedly help in meeting the increasing demands for accuracy and consistency in machining processes.